A place to share YOUR boat building story
Glen-L Marine Designs - 9152 Rosecrans Ave. - Bellflower, CA
90706
In this issue
GLEN-L
Update
-
All of us here at Glen-L really appreciate every photo you
send us of your boats, whether it be in the construction
phase, the finishing phase, or that wonderful time when
you finally get to put her in the water. We especially
look forward to the photos you take that show the result
of all of your efforts as you are out on the water with
your family and friends. Those of you who have completed
your crafts know the special feelings of pride and
accomplishment you get from the looks of admiration when
you tell people "I built her myself."
-
To that end I want you to know that I am working every day
to get all of your photos up on the website. If you've
submitted photos and haven't yet seen them posted
it's only because there's a bit of a backlog
that's taken me longer than expected to clear, not
because we don't value every photo you've
sent to us.
-
I sincerely hope each of you who are building one of our
boats, or have completed one (or more) will take a couple
of minutes to write and tell us a little about your
feelings and experiences, dreaming about, building, and/or
enjoying your boat. THESE are the stories that
really make these WebLetters fun and interesting -
"inquiring minds want to know", you
know.
-
I don't know the origin of the quote, but I've
seen it ring true over and over again:
"A sorrow shared is a sorrow halved, but
a pleasure shared is a pleasure
doubled."
Won't you double your pleasure by sharing your
stories with us?
Until next month . . .
Editor
2008's Top Boat Names
FirstBoat.com has announced its
list of the most popular boat names of the past year. The
list includes nautical puns, tributes to recent movies and TV
shows, and an overall celebration of the boating
lifestyle.
Here are the top ten most popular boat names for 2008:
-
Happy Ours
-
Carpe Diem
-
Aqua-Holic
-
State of Mind
-
Anchor Management
-
The Office
-
Feelin' Nauti
-
Yes Dear
-
Sundance
-
Serenity Now
Several of the boat names on the list, such as "Happy
Ours", "State of Mind" and "Carpe
Diem", reflect how much enjoyment people derive from the
boating lifestyle. In fact, the popularity of these particular
boat names may suggest that boating, for some, offers a
temporary respite from the unremitting news about a distressed
economy and record-high fuel prices which were experienced
during the peak of last year's boating season.
In general, most of the names on this year's list of top
boat names illustrate that boaters are imaginative and
passionate individuals who like to have fun.
Glen-L Boatbuilder of the Month
George Redden - Malahini
George finished his Malahini in August 2007 and launched late
that month and tells us "she runs very well. The 60-HP,
4-stroke Mercury outboard is exceptional; instant start,
smooth, quiet, nice idle operation and pushes the boat to 40
mph at max revs of 6600 rpm (fast enough for me!)."
"The hull is finished with Interlux black paint, decks are
mahogany planked - caulked white topped with Interlux Goldspar
varnish, upholstery is pleated forest green vinyl, and Faria
gauges in a mahogany dash."
"The most common onlooker questions are 'What year is
it?' and 'Is that an old Chris Craft?' I stopped
varnishing at seven coats so that the Honduras mahogany looks
like real wood and not something buried under fifteen coats of
plastic."
George says "The cockpit layout has proven to be very
good, except I should have made the walk-through four-inches
wider. It is difficult for me to kneel down when accessing the
bow storage compartment, which holds the homemade cockpit cover
and auxiliary gas can. The mid hatches are fitted out to hold
fenders, docking lines, cooler, waste container, fire
extinguisher, etc. The aft hatches give access to the fuel tank,
battery, bilge pumps, general storage and the auxiliary
electrical panel with battery manual switch, pump fuses and
hour-meter. The bottom of the back seat is hinged for storage
under it with racks for the boat hook, boarding pole, and
cockpit cover support."
"Betty and I will be entering a few ACBS shows this summer
and we'll let you know if anything eventful
happens."
"Happy boating!"
-- George & Betty Redden,
Staunton, Virginia
Editor's Note:
See more about George & Betty's Malahini
in the Project Registry and in Customer Photos.
Featured Design: Bandido
The BANDIDO is a 30' luxury offshore
performance boat offering high-tech performance and
construction methods to match the exotic production boats, at
a fraction of the cost. You can build yours in Wood or
Fiberglass with a wide array of powering options. The
trailerable hull, capable of 50+ knot speeds in offshore
conditions, features a 22º minimum deep vee with
radiused keel section and lift strakes.
Your BANDIDO can be set up with single or
twin inboards (either diesel or gasoline), driving through
I/O units, vee-drives, surface propeller drives, or with jets
(with minor modifications). Or use twin outboards if you like
(a single outboard engine is also possible). The choice is
yours, and a large fuel capacity means long range even with
larger motors.
Because of the high performance potential of the BANDIDO,
construction is aimed at the conscientious builder willing to
follow instructions and use the best materials. With the Wood
Version, we specify cold-molded wood veneers or plywood
strips laid up in multiple layers diagonally applied, all
bonded together preferably with an epoxy bonding and
encapsulating system. A layer of fiberglass on the exterior
is used for abrasion resistance and added durability. A
carefully designed structural "grid" framing system
emphasizing longitudinal stringer webs makes a strong, yet
lightweight hull.
With the Fiberglass Version, several materials and
"one-off" methods are detailed, depending on the
builder's budget, abilities, and desires. The fiberglass
planking option is probably easiest and cheapest of the
fiberglass methods for the novice, but not the lightest in
weight. The sandwich core option, using a core material of
PVC foam or end-grain balsa, is perhaps a bit more costly,
but somewhat lighter in weight. Both systems result in strong
boats well within the average amateur's abilities.
The High-Tech version is for the builder who wants the
ultimate in light weight and performance potential. The
fiberglass hull consists of a sandwich core using rigid PVC
foam or end-grain balsa. The super-thin high strength skins
are made from aerospace-type S-Glass uni-directional and
triaxial fiberglass reinforcements. The high-tech version can
be built using conventional "one-off" methods, or
for the more adventurous type, vacuum bag methods suitable
for many amateurs more fully explained in our text, FIBERGLASS BOATBUILDING FOR AMATEURS.
This system can result in a structure that weighs less than
2000 lbs! Procedures used to build the high-tech version are
not any more difficult than the other methods; they do,
however, require care and attention to detail.
Regardless of the construction method, all BANDIDOs feature
a plush cabin with galley provisions and a head, a spacious
and safe cockpit, and a roomy sun deck lounge. All plans
include Full Size Patterns and comprehensive instructions to
simplify construction.
So why wait? Fulfill your dream now and save thousands.
Designer's Notebook: Make Your Own Hardware
Although pattern making
for complex parts is still best left to the pros,
making a wooden pattern to then have a foundry make
a metal sand casting is well within the abilities of
the typical DIY individual. Making a water-cooled
exhaust manifold is usually well beyond the
DIY'er, but simple cleats or one of a kind
fittings are mostly within the realm of the handy
person.
A basic understanding of how a foundry makes a sand
casting should be understood. The "sand"
used to make the casting is a special product and
not the typical beach type; clays and other
additives make it stick together.
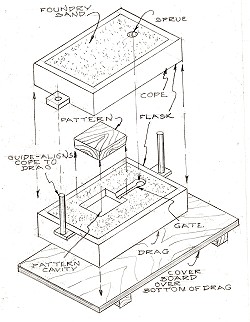
For example, let's take a simple flat plate
pattern as shown in the sketch. Note that the sides
are tapered (this is called "draft"); the
part must be able to be withdrawn from the sand
mold. The person who makes sand castings is called a
"molder". He uses a two part box called a
"flask" to hold the sand mold. This flask
is divided into two halves, aligned by guides; the
flask does not have a fixed top or bottom. The lower
part of the flask is called a "drag" and
the upper section "cope".
Using the simple flat plate pattern, the molder
lays it on a flat board. The drag portion of the
flask is inverted over the pattern lying on the flat
board and the molding sand packed firmly over the
pattern and into the flask drag. Another flat board
is put over the exposed open end of the drag and the
entire affair rolled over and the original flat
board removed to expose the top of the
pattern.
The cope (upper half of the flask) is slipped over
upright locating pins and the cope firmly packed
(rammed) with sand. A flat board is put over the top
open end of the cope. The cope is then slid upward
by the guide pins and off of the drag. The cope and
board are then flipped over so the part with the
pattern impression is exposed.
The wooden pattern is then carefully withdrawn from
the sand mold. A good molder will draw the pattern
from the mold with almost no sand being disturbed.
The molder cuts "gates"' (paths in the
sand) for the molten metal to enter the pattern
cavity. A "sprue" or hole for entrance of
the molten metal is cut through the cope sand
directly over the gate in the drag. The mold cavity
and gates are cleared of any loose grains of sand.
The cope is then inverted and placed over the drag
with the guide pins aligning the two.
The sand mold is then ready to be poured with
molten metal. After cooling, the casting is removed
from the sand, the gate cut off, and you have a
metal duplicate of the wooden pattern.
The resultant casting will be smaller than its
pattern. In manganese bronze the difference will be
about 3/16" to the foot, but this will be
unimportant for the typical cleat or similar
fitting. If, however, the part being made is to fit
to another part, shrinkage should be allowed for.
Special "shrink rules" are available but
calculating the amount of shrinkage is not that
difficult.
Wooden patterns may be made from almost any stable
wood; soft white pine is easy to carve and for short
runs is commonly used. The important thing to
remember about a pattern is that it must be pulled
from the sand mold smoothly; it must be tapered or
have draft, no back hollows. A pattern may be split
in two halves with the "parting" line on
the same plane as that of the cope and drag
junction. In truth, the parting line does not have
to be in this plane but to keep things simple,
we're describing a pattern that has the above
requisite or is in the drag only as our flat plate
example.
Examples of split patterns.
On the left is a split pattern that was made to slip
over a boom tube of a very small dinghy. The split
pattern halves are aligned by small dowel pins
tapered to slip out easily but align the two halves
accurately. On the right is a fitting made for the
bow of a sailboat. The forward portion is a cleat
while the aft vertical portion can be drilled for
the forestay pin and other fittings required.
Sharp corners cannot be tolerated on sand cast
patterns. Interior junctions should be filleted,
made from any hard setting compound that can be
easily applied and formed. Fillet shape wax is
frequently used by pattern makers but since small
quantities may be difficult to obtain, for small
patterns paraffin wax will suffice. A heated fillet
tool (simply a steel ball on a handle) is used to
apply fillet wax, melting it and forming it into a
junction. Just be certain all edges are well rounded
and all junctions flow smoothly together with draft
or taper.
The finished pattern must be sealed. For years
orange shellac made from scratch was used. Sand
mixes became more complex and special coatings were
developed but are expensive and difficult to obtain
for most. Lacquer-based finishes also work well.
Usually two or three coats of paste wax, well rubbed
over the pattern, will suffice for short runs. If in
doubt, check with the foundry that will make the
part.
Sand castings for marine use are generally made
from a brass compound, red brass, manganese bronze
or related alloys. Aluminum is easy to cast but does
tend to deteriorate, especially in a salt-water
environment.
The patterns shown are but a couple of examples of
what can be made from sand casting patterns.
We've made patterns and sand castings for most
anything that can be imagined; cleats, lifting eyes,
bow handles, vents, hawse pipes, exhaust port
flanges, water pickups, steering wheels and columns,
throttle fittings, windshield brackets, struts,
fins, rudders, etc. Some parts will have back-draft,
holes, or other conditions that may need to be free
of molten metal. An insert in the mold cavity must
be used called a "core" that is made from
special sand packed into a wooden core box, removed
and baked in an oven. The resultant core is inserted
into the mold cavity.
This short discourse is not intended to cover the
pattern nuances required for patterns with cores; it
can be a complex subject. The would-be pattern maker
contemplating making patterns that require cores
should obtain a good book on pattern making and
foundry practice.
The handy DIY person can make simple parts,
however. It's fun and castings can be made for
parts that can't be bought but do fill a
particular need.
Try it; you'll like the challenge and end up
with a one-of-a-kind part or fitting.
|
Anchors
A nchors are as old as
boats
According to ancient lore
They hold on to the seabed
And keep you off the shore
Some have flukes to dig in
Others work by mass alone
Some are permanent moorings
For anchoring at your home
For temporary holding work
There are anchors of many types
Danforth, Northill or Claw
Will all fit in your hawse-pipe
Some say for better holding
Go with a mushroom or a plough
Though breakout can be difficult
You’ll need strong cleats on the bow
Some older types I’ll mention
The stockless, fisherman or screw
Not often seen much anymore
But in a pinch, they’ll do
The simplest kind of anchor
For use on a small boat
A paint can full of concrete
Or just a rock and a rope
Whatever type you choose
To hold you in wind and sea
Be sure to tie the bitter end
If you lose it, don’t blame me
-ArtDeco
|
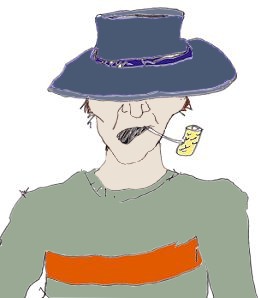
"Wish
not so much to live long as to live
well."
--- Benjamin Franklin, 1746
(rumored to have been said whilst building his
first Glen-L designed boat)
|
Shop Talk: Clever Tips
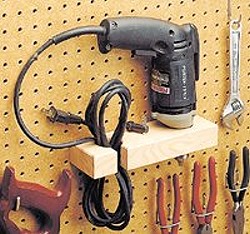
Drill
Holster
Here's a handy way to store your electric drill, sent in
by Dick Grote of Palo Alto, California — a
"holster" that hangs on a pegboard rack.
The holster is a scrap of "two-by" material with
two openings cut in it. The drill chuck fits in a large hole.
And the power cord slips into a keyhole-shaped notch.
By installing two L-hooks in the back edge, you can hang the
holster securely on the pegboard.
Assembly
Blocks
Sometimes you almost need a third
hand to assemble a project, especially working with large
pieces of plywood. To help keep the pieces aligned, use
assembly blocks made from scrap.
Make these blocks from medium density fiberboard (MDF) with
intersecting dadoes cut in the middle (pieces of plywood or
solid wood would work as well). Just set the workpieces in
the assembly blocks or place the blocks on top to hold the
pieces in place until the clamps are installed.
Recent email:
Subject: Boatbuilder Forum
Date: 12 January 2009
I just discovered the forum!
Nice job on the WebLetter (love the Jimmy Buffet
song, too)!
-- Ray Boller
Subject: Outrage
Date: 14 January 2009
I sent you a Power Point presentation of my building the Outrage.
I've built 4 Glen-L boats - one sailboat and two copies
of TNT and now the "Outrage." This
one was the most fun. I am an architect, but my hobby is
cabinet making.
Your plans are very accurate and easy to work with. I would
recommend them to anyone that is ready for a boatbuilding
project.
-- John Wilmot
Edgewater, Maryland
Subject: Great Information
Date: 22 January 2009
Thank you very much for the information you gave me. My Glen-L
books arrived the other day and I've been reading like
crazy; I'm definitely inspired to build my first boat!
-- Brad Lynskey
Arkadelphia, Arkansas
Subject: Glen-L Website
Date: 27 January 2009
Your website is fascinating! I hope I can find some time this
weekend to take a closer look.
I have great childhood memories of helping my grandpa wax and
polish his 1950s Chris-Craft speed boat. Maybe that's why I
hang a new Wooden Boat Calendar up in my office every
year...
-- Andy
EZ Woodshop.com
Editor's Note:
You'll find Andy's excellent website
Andy's EZ Woodshop quite
interesting.
Subject: Acapulco Camper
Date: 27 January 2009
Hi there. I started building the Acapulco Camper in the fall of 2008. I have
built most of the shell and am now working on the roof. This has
been a fun project so far; I will send photos soon.
Thanks for the great plans.
-- Steven Gourley
Trenton, Ontario, Canada
Subject: "Build Your Dream Boat" Newsletter
Date: 25 January 2009
Gayle,
You deserve a marketing award of some type. I smile when I see
Glen-L eMail in my inbox - your messages usually arrive just
when I have talked myself out of a boatbuilding adventure.
And through some psychic ability you always seem to hit the
points I've used to talk myself out of it.
-- John Haley
Henrietta, New York
Subject: "Ribs Up" Party
Date: 1 February 2009
Aloha...I ordered your Mist Miss drawings in October or November,
started building on December 1, 2008 and had my "ribs up
Party" last week.... will send you some photos in due
course. Aloha.
-- Jack Waggoner
Sacramento, California
eMail of the Month
Subject: Thank You
Date: 27 January 2009
Dear all at Glen-L, thanks for all the information
that you sent. My project is going slow, but it is
going. Stem is connected to the breasthook, side
braces are done, transom is half way and hopefully
will be ready for mid-February when I plan to build
the platform.
My big problems are second floor flat, no garden,
no driveway, and two girls that are in education
(the girls are not the problem but paying for
education is). But hey, life is too short for
negative attitude, so we will do it.
Oh, sorry, my name is Alex, I live in London, and I
was born by the river Danube in Serbia. In the
eighties my brother and I built a 13-footer in
plywood and fiberglassed it with polyester, but I
always wanted to build with epoxy, and this Power Drifter is just an
educational exercise. Plan is to build a classic
sailing yacht in cold molding, and Mediterranean
retirement.
Dreams. Yes dreams. Smell of wood when cut or
sanded, dreams become reality. Freedom at last.
Thank you.
Wishing you well.
-- Alex Bekvalac
London, England
|
Build more boats
GLEN-L boats, of course
|