A ZIP-Builder's Diary (Cont'd)
by Dave Coleman, San Francisco Bay Area, California
Chines - The port chine
didn't land on the stem with the right twist so I had to
add a little beveled shim to make a flat landing place. Not
sure if they land at the right place on the stem but the
notches in the plans seem to encourage the wood to land where
it lands.
Sheers - Had a bit of
struggle with cracking. I'm using Yellow Alaskan Cedar
for the longitudinals. The towels and boiling water technique
seemed to work, relaxing the wood and allowing both
laminations to bend at the stem. But I think after I got the
first lamination in place I let too much time go by and the
second one dried too straight. It cracked when I re-bent it.
My fix for the first crack was to epoxy and screw the crack
together and move the cracked place to the stern where it
would be straight. I had some other smaller cracking later
which I epoxied in place. It looks shabby but when it's
all put together I think it will be fine. If I were to do it
over, I'd make 3 or more laminations.
Epoxy - I'm using TAP
Plastics Marine epoxy for gluing (slow curing since it's
been a little cool here and it's good down to 40° F).
I mix small batches in Zip-Loc bags, snip off a tiny corner,
and squeeze it out. It seems to be working OK but I still end
up with epoxy on my hands. Yeah, I know, use latex gloves.
That's OK too but it still gets all over the tools.
Side Planking - I'm
using hydrotek 1/4 inch ply. I butt-joined the 8' lengths
in advance of putting it on the boat. Seemed to work OK
without screws. I found that bending the plywood at the
transom is much easier with a minimum of excess ply
projecting back. I was struggling with the bend before it
dawned on me to whack it off. For bending the second side at
the stem I had to screw down some blocks for something the
clamps could pull on. I remembered most of the time to erase
(sand away) pencil marks on the plywood before epoxy could
drip on it and enshrine the marks forever.
I've countersunk the screw holes joining to the sheer
pretty deep with the idea of plugging. We'll see how that
works out. If it's a bust (or too much work) I can paint
a nice stripe at the gunwale as someone else has done and
still have a lot of nice mahogany showing.... Well the plugs
I used on the port side were too light colored. I gave up on
the idea of staining them. Too much work and too messy, plus
I may end up painting a stripe or having a large enough rub
rail to cover them. I used Sipo plugs on the starboard and
they looked much better.
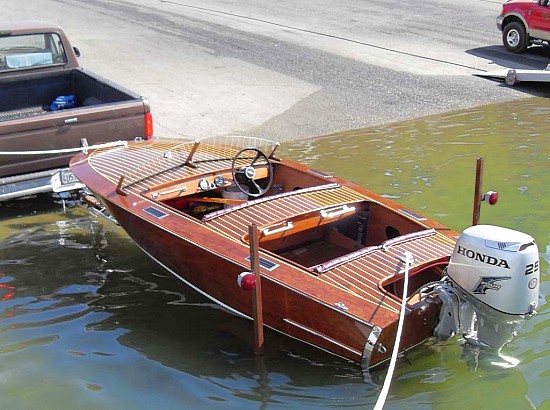
Bottom Planking - I butt
joined after the forward bottom pieces were in place. The
forward bottom pieces took a bit of fussy fitting because
they have to butt to each other and to the sides. The famous
transition between lap and butt went fine. It's all going
to be filled and painted anyway. The aft bottoms were pretty
flat and easy.
Before I put the bottom plywood on, I did manage to remember
to unscrew where the building frame is attached to my plywood
floor with vertically oriented screws. I figure I'll be
able to reach the horizontal ones when the boat is
covered.
Donor Boat - I watched on
craigslist for a derelict runabout with trailer. The goal was
to use the trailer, deck hardware, outboard controls, and
even the windshield if I get lucky. I got a response from my
boat-wanted ad and a guy in the sailboat salvage business
delivered to me a 16 foot boat with trailer for not much
money. I stripped the boat of usable parts, cut it up with
the sawzall, and took it away in pieces. I stripped the
trailer of old bunks, verified the wheel bearings were OK,
adjusted the movable dimensions for my boat, and installed
new bunks. In the end I couldn't use the steering box and
cable, nor the outboard controls or windshield. But I did use
the wiring harness, steering wheel, fuse panel, speedometer,
and lots of deck hardware.
Glassing & Epoxying -
I saw on the Boatbuilder Forum a reference to the
fiberglassing technique where the fill coat is covered with a
polyester (Mylar) film. When the epoxy is cured the film is
peeled off to reveal a perfectly smooth finish with no cloth
poking through or need for sanding. The forum chat seemed to
be it was too good to be true. But to me it's also too
good to ignore. I tried it on some scrap and it worked
wonderfully. I was told by the old guy at TAP Plastics that I
have to remove the film before 24 hours or it might not come
off. My test showed it didn't come off after 6 hours
(apparently not cured enough in my 50°-ish garage), but
it did come off well after 9 hours, again at 18 hours, and
again at 28 hours. So I think I have a good range of time.
I'll try the transom first.
My neighbor and I did the transom this morning and I peeled
off the film just now. It's quite shiny, flat, and
wonderful. It took 4 hands to do it. I squeezed the epoxy out
of a Zip lock bag and applied it with a squeegee. My neighbor
followed about a foot behind with the roll of Mylar and
squeegeed out the bubbles.
Used the same technique with the first bottom half, but we
got bad ripples under the film that will need to be sanded
down, then have a finish coat applied. Our conclusion was
that there was more resin as compared to the transom.
We'll try it with less resin on the other bottom
half.
No luck with that half either. My conclusion is that the
film only works on small, very flat areas. And after lightly
sanding the "wonderful" transom, glass and voids
started to appear. All in all it took more work and I would
not recommend the approach. I used the textbook approach with
the sides. They took some sanding, but not a huge amount, and
they look great after varnishing.
Cutwater - I would have
preferred stainless, but my resource for doing it
economically pooped out so I decided to do it myself with
copper. The copper I was able to get was only 24 gauge
(roofing flashing stuff), so my neighbor and I came up with a
method of sandwiching two layers. The bottom layer had
interlocking tabs which made a solid structure and held the
shape it was given, and the outer layer was the smooth one. I
did cut out a hole for the bow eye, so the cutwater can be
installed later (much later), and so pulling on the bow eye
won't pull on the cutwater. I sanded and polished it and
the two stern pieces and got them chrome plated. They came
out shiny and quite impressive.
Motorwell - The specs
called for a rather large well and since I am expecting to
deck most of it over I extended the depth to end at the rear
seat support. I think this was an OK approach since I still
have just enough room under the well for the battery. It
turned out I needed the full 33 inches of width for the
steering arm, but I will be able deck over about half of the
depth.
Transom Cutout - Mine
measured 15 inches exactly, and I bought a short shaft motor
where the specs said it took a 15-inch transom height. Then
to my surprise, the motor measured 17 inches. So I added 2
inches of height with some sandwiched plywood and a backer
piece of 3/4 inside the motorwell. I guess the moral of the
story is to measure the motor yourself way in advance.
Dashboard and Steering -
The new steering box has a 90 degree mount so I angled the
dashboard about 20 degrees to give it desired tilt. The
steering box takes up quite a bit of room so I had to do some
fussy fitting to get it to the right height, etc. I figured I
would have to remove the dashboard later to fiddle with
gauges etc. so I cut it into two pieces so I never have to
mess with the steering again.
Things are pretty tight behind the dashboard, but I managed
to get the salvaged speedometer and a new tachometer
installed, together with a switch for nav. light, a switch to
force the bilge pump, and a 12 volt outlet. It looks pretty
good to me.
Interior and Floor - I
probably ruined the boat, but to make the small boat as
comfortable as possible for people with legs, I cut back the
frame gussets so they wouldn't be sticking out over the
floor. The floor is 3/8 inch plywood and now covers the bilge
nicely except forward of the front frame and aft of the back
seat. I've tried to make it removable with screws
accessible and pull-up handles so I won't need to pry it
out. For cockpit sides I used 1/4 ply except for one with 3/8
(plus 3/8 backing) for mounting the controls. Each panel has
a big cutout for storage, access, and control cables. I made
seat boxes to give a little height and used 3/8 ply for the
removable seat and back pieces. These get upholstered
later.
Electrical - I was able
to use the battery switch, a fuse panel, and a long piece of
wiring harness from the donor boat. I've got most of the
wiring done now except for the deck-mounted items.
Decking - This is the
exciting part. For each side I cut out a foredeck piece, a
center deck piece, and a stern piece. It took three sheets of
plywood since the foredeck pieces are so big. The overall
approach is to cut slots in the 1/4 inch plywood to fill with
pigmented epoxy paste to get the desired white stripes. I
routed the slots with the plywood off the boat (laying flat).
The #8 screw heads are pretty wide and I wanted to fasten
through the slots as much as possible and I wanted narrow
slots. So... I probably violated all boatbuilding rules - I
fastened the deck using galvanized staples, as well as epoxy
for glue. It sure was easy and fast to shoot the staples to
fasten to the longitudinals versus putting screws in to
fasten at the sheer.
Outboard Motor - Other
boats I've owned have been inboards so these delicate
little outboard creatures are new to me. After mounting the
new Honda 25 4-stroke on the boat, the dealer warned me about
using new fresh gasoline and running the motor dry before
storing it. I took the boat home and got back to work on the
wood, ignoring the motor until just now (6 weeks later) when
I tried to get it going again. It started but ran very rough
and died frequently. So I changed the gas, put in some
Sta-Bil and some cleaner, and ran it a lot today and it
improved a lot - though not yet back to its original
perfection. So, another lesson for this old boy.
Rub Rails - I bought 3/4
inch hollow stainless rails from West Marine and my approach
is to rip some 3/8 by 1 1/2 mahogany strips and dado 3/4
slots to contain the stainless. The real Honduran Mahogany is
a treat to work with, straight fine grains and not too hard
to rip 1 1/2 in one bite on my portable table saw. But
bending it was another matter. On one side I tried steaming,
but either I didn't do it enough or what I was asking was
impossible because I got lateral cracks in the center of the
strip. The crack will be covered by stainless, so no worries
there. For the other side I cut 4 to 5 inch lateral slits and
the kerfs at the bottom to relieve the slits. It bent pretty
readily, but got some flat spots that needed fairing. The
wood is a lighter color that makes a nice contrast to the
dark sides and deck "planks".
Decking Stripes - I
filled the slits with epoxy colored off-white. This required
masking all adjacent surfaces, which was very tedious but
necessary. I mixed thickener with the pigment into the epoxy
and squeezed in on from zip-lock bags. The difficulty was
getting the thickener mixed in well enough and several places
came out kind of lumpy. After glassing and more epoxy, the
lumps are pretty well disguised, but there is some color
variation. In retrospect, I would mix the thickener in with a
stick in a small tub, and then transfer to a bag.
Glassing the Deck - I
bought 4 oz cloth in 50" width and covered 1/2 of the
entire deck at a time with the join at the center. It went on
well, and the glass seemed to mask well the lumpy surface of
the stripes. The stripes have yellowed a lot since they were
put in, probably due to UV exposure. They look good though
and I'm happy with the color. I put on a total of 4 coats
of epoxy, sanding it down to (fairly) flat after the last
coat. The neighbors would see the epoxy go on and be excited
by the shiny dark appearance. Then I'd rough it up again
with the sander. Now finally I've put on the varnish and
to me it looks great.
Deck Hardware - This is
the fun part, adding the "bling". I through-bolted
the fore and aft cleats but the other stuff is just screwed
on.
Windshield - I decided to
make my own brackets. I used a piece of Ipe (Brazilian
Iron-wood) that I had left from a decking project. It's
very hard and heavy and it seems quite strong. I made two
brackets for the center rather than having to route two deep
grooves in the same piece. I attached pieces of rub strake
stainless to the fronts of the brackets and they look pretty
good. When I had the 1/4 inch laminated glass pieces cut, the
glass guy warned that any pull on the glass or even wind from
fast travel could flex the glass and break it. He recommended
a solid (wooden) trough to support the bottom. I spent some
time ripping and routing and found that there was no way the
wood would bend to accommodate the edge curve of the glass
and the curve of the deck. So I've ordered some
specialized flexible gasket material from the only place I
could find on the web.
Registration Numbers - I
ordered vinyl numbers off the web and mounted them per the
instructions. The numbers look fine, though if I were to do
it again I'd try to get them curved downward at the ends,
or cut them apart for mounting. As they are, straight decals
mounted on a curved surface, they curve upward at the ends
looking a little goofy. Another possible complaint is that
gold letters with black outline don't show up with much
contrast on a dark mahogany hull. I don't mind but some
state bureaucrat might.
Outboard Motor - When I
bought the motor, the shop asked me about the age of my
gasoline. I wasn't sure but we started it anyway and it
purred like a kitten, idling so smoothly you would hardly
know it was running. So I took it home (on the uncompleted
boat) and continued with my boatbuilding for several months.
When it came time to try out the controls it would hardly run
at all. I've tried several approaches to no avail. It
still runs somewhat rough. It's my own damned fault for
letting the initial rather aged gasoline evaporate in the
carbs. So I may have to confess my stupidity and pay the shop
to clean the jets.
A mechanic friend looked at the motor. He also thought it
looked like a lot of work to remove the carbs to clean them
but would help me do it if necessary. He suggested first that
I run a strong solution of cleaner in the gas for a while,
then let it sit with the cleaner in the bowls for a couple of
days. He also increased the idle speed. I ran it as
suggested, and though still not perfect it was good enough to
try in the water. When I called the motor shop they suggested
that I take it out and run it hard for a while in hopes it
would straighten out.
Launching - The neighbor
who's helped me with the boat, a son-in-law, and I took
it to a local lake, put it in the water, and gave it a good
try. It was quite successful by all accounts.
The motor seemed to straighten out and run OK. It got up to
about 25 MPH at 5600 RPM. We ran it for just over an hour at
various speeds. It sits in the water a bit down at the stern,
and about the same with three men on board. When the throttle
is applied the stern goes down a bit more but not alarmingly,
then at just under 20 mph it levels out nicely on a plane.
Revving it up to 5600 takes it up to about 25 MPH. More revs
don't add much.
Turning hard at speed induces cavitation (ventilation -
whatever) and the boat slows down. I adjusted the motor tilt
to full down (nose down). That seemed to help the cavitation
but reduced the top speed. Next time I'll try it tilted
up two notches and maybe get more speed, though one notch
seems OK and I figure I can just turn a little more gently.
With my 2 inch skeg there is no side slip in the turns.
The boat is pretty dry. The stern passenger doesn't get
sprayed at all. A dribble of water came out of the bilge
drain after we pulled it out, but the bilge pump never had
enough to pump.
When we got back we were able to roll it up (on the trailer
of course) onto the deck where I built it at the side of the
house so it's not taking up driveway space anymore.
So it's ready for Tahoe, though a bit late for this
year.
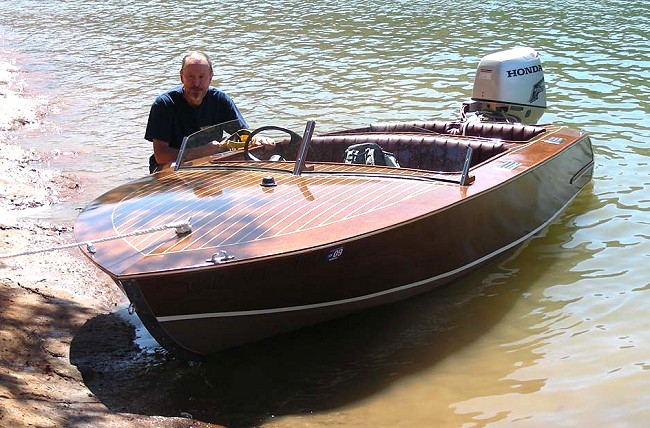
The project was great fun and I'm quite proud of the results.
Complete Project Photos and Commentary
|