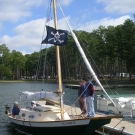
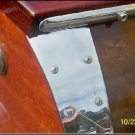
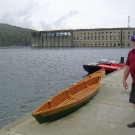
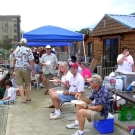

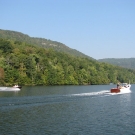
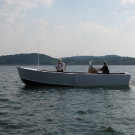
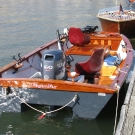
Steel is an excellent boatbuilding material, proven in use worldwide. However, due to the relatively high weight compared to other boatbuilding materials, and the care required in the design stage with regard to hull development, structural integrity, stability, and balance, the plans used to build a steel boat should be intended specifically for use with this material.
Using plans for a design intended for some other material and converting it to steel should not be done, at least without careful (and usually costly!) redesign by a qualified naval architect. That’s why GLEN-L has developed a series of low cost stock designs intended for steel construction in our online store.
For the amateur boatbuilder who has knowledge of proper weld types and welding sequences, together with the necessary electric and gas welding skills, steel is an ideal material. On a cost-per-square-foot basis, steel is probably the cheapest of all boatbuilding materials.
Construction is simple when using the building methods specified in GLEN-L plans, and faster than just about any other boatbuilding material. No special shelters or structures are required, and the materials are readily available just about anywhere without special order. For strength, steel is just about tops in all respects. Repairs and modifications can be easily made anywhere in the world as long as a welding set is available.
Even if you don’t know how to weld, acquiring the necessary welding skills is relatively quick and easy. Numerous welding schools and classes are available in most areas, either through public school systems or through private trade schools. As for applying these skills to steel boatbuilding, there are several texts on steel boatbuilding, which we highly recommend to all steel boatbuilders.
To further put steel boatbuilding within the realm of the amateur, ALL GLEN-L steel boat plans include our comprehensive “STEEL BOAT-BUILDING GUIDE” to supplement the plans and abilities of the builder. This general instruction manual discusses the various building procedures and options for setting up, proper hull assembly sequence, welding recommendations, tank construction, insulating methods and materials, joinerywork, electrical, finishing, and much more.
To enable the builder to fabricate many of the usual “store bought” parts, the plans are further supplemented by numerous detail sheets showing hatch construction, rail details, rudder fittings, shaft tube and stern bearings, mast steps, chainplates, deck details, cabin-hull junctions, and joinery details.
Full size patterns mean even faster construction since no lofting is necessary. For those who desire to loft their boats, however, a Table of Offsets is also provided. And of course, our comprehensive plans include all the typical information you’d expect to find in a GLEN-L plans set.
They cover all aspects of the design including structural views and sections, scantlings, cabin construction, joinery arrangements, tank configurations, engine placements, rudders and underwater fittings, and spars on sailboat designs. In short, you get everything you need in the way of information to build your very own steel boat, and at a low price! That’s why at GLEN-L we mean it when we say, “You get custom design quality at low stock plan prices.”
See our Online Store for all the steel designs by Glen-L Marine.
The steel used is normally mild (plain low carbon) steel of welding quality, although corrosion-resistant grades, such as “Cor-Ten” (a trade name) are optional but more expensive and hard to work. Steel is usually sold in quantity by weight. That’s why for each steel design we provide an estimate of the weight of the steel hull components. Simply use this figure times the cost of steel per pound in your area to arrive at a reasonable estimate for hull material costs.
Aluminum is also a superb material for boatbuilding by the person qualified in aluminum welding. Aluminum boats using welded marine alloy construction are strong, lightweight, durable, and easy to maintain. As with steel, the designs should be specifically intended for this material.
Plans listed for aluminum construction include all the details necessary to build the boat in sheet aluminum. As with all our designs, they include FULL-SIZE PATTERNS so that no lofting is required. In addition, all aluminum designs include our comprehensive “ALUMINUM BOATBUILDING GUIDE” as well as a hull material listing. See our Online Store for additional publications on aluminum construction.
Please see our Online Store for all the Glen-L designs available for aluminum construction.
The following can be used as a general guideline for selecting materials. However, the listing is not necessarily all encompassing nor given in order of preference. To figure hull cost, use weight of hull times cost per pound.
COMPONENTS & MATERIAL Hull plating and decking 5052-H32 to H36 5086-H32, H34, H112 or H116 5456-H116 Framing 5052-H32 to H36 5086-H32, H34, H112, or H116 5050-H34 or H36 5456-H116, 6061-T6 Extrusions 6061-T4 or T6, 5086 5052, 6061-T6 Piping 6063-T6, 5456-H116
When buying aluminum sheet or plate goods, the terminology “sheet” refers to material of .188″ or less (nominally 3/16″ or thinner), while the terminology “plate” refers to material .25″ (1/4″) or more.
For further information on welding, see WeldingTipsandTricks.com.
The number of people with aluminum welding skills and access to fabricating equipment has increased considerably over the years. Yet many are unaware of fundamental considerations confronting the short-handed amateur building a single boat for his own account. I’ll discuss many of the more common issues, especially as they relate to powerboats in the 15′ to 40′ size range we most commonly deal with today.
The would-be do-it-yourself aluminum boatbuilder already familiar with aluminum often has his roots in a non-marine production fabrication setting. Thus there may be a tendency to want to apply mass-production techniques to the construction of just a single boat. But building a single boat yourself is considerably different from one built on a production line, and thus may require certain adjustments and even a revised mind set on the part of the builder.
First, there is no one, superior way to build an aluminum boat. In fact, there can be many suitable approaches and variations. Second, there is no reason why you can’t build your own aluminum boat in your own garage or backyard that looks identical to one produced in a factory, and with similar weight and strength qualities even if you don’t use the same mass production methods, or have access to sophisticated, specialized equipment and proprietary materials. Consider the following.
Because production builders are always thinking up ways to cut labor and material costs, and time required to build boats, they evolve specialized methods and materials that help toward these ends even if there is not necessarily any improvement in the boat itself. For example, they may use special proprietary extrusions to expedite some assembly process such as joining side and bottom plating at the chine (see Fig. 1E).
But when building your own boat, you may not have access to such a specialized member, nor could afford it or the shipping in the small quantities you’ll need even if available. Alternately, your chines might then be backed with a simple round bar (Fig. 1D) or other standard shape, or the plating might simply butt together and be welded(Fig. 1A). None of these methods is necessarily superior, but just different due to circumstances.
Also, production builders often make up sophisticated re-usable production jigs over which pre-cut hull panels are assembled and welded first. These jigs may also rotate to facilitate high-speed welding, with internal members added after the hull is removed from the jig.
But when building your own boat at home, it’s just as likely that the boat’s internal framework gets built and set up first, with plates fitted over this, marked to shape, cut to suit, and then welded in place after. In other words, the boat’s framework becomes the forming jig and stays in the boat; you make it and pay for it only once. In either case, end results are much the same and with comparable boat quality.
Using a frame substructure for setting up your hull has several advantages for the do-it-yourselfer typically working alone. First the frame substructure makes it easy to assure hull accuracy that is so important to ultimate performance in a powerboat. Second, the framework makes it possible to build from “off-the-shelf” materials and shapes available anywhere for lower costs and easier material purchasing. Finally, the framework makes it easier to form hull members in place and during weld-up since clamps and other devices can be readily used most anywhere as required, acting as extra pairs of “helping hands” in the process.
Factory production boatbuilders often use specialized forming equipment not always available to amateurs, or use forming services that might be provided by metal suppliers when quantity requirements are high. For example, special rolling and/or bending equipment might be used to form integral shapes in hull plates for stiffness, etc.
Conversely, a design for the do-it-yourself builder would more likely specify internal longitudinal stiffeners (i.e. flat bars, tee’s, angles, etc.), and be designed in such a way (as we typically do) so that no special forming or bending equipment or outside services are required. Either method gets the job done but the latter is easier and cheaper for most building their own boats.
First, a disclaimer. Ideally, when converting a design in one material to another, one should seek the advice of a qualified designer or professional naval architect to make the modification, or at least consult with the boat’s designer as to the feasibility of such a change. But in reality few do-it-yourselfers want to pay the price for the service.
So if you can’t find an aluminum design of the size and type you want, you might check designs in steel – the closest material alternative. But steel is considerably heavier than aluminum, so boats designed for steel are usually designed for greater displacement. Thus, if the boat is built from aluminum, it won’t be nearly as heavy and may therefore float higher in the water. The consequences for a semi- or full-planing powerboat might be so much the better since the lighter aluminum boat will need less power and fuel.
But in converting slower displacement-type powerboats from steel to aluminum, you might need to add ballast into such a boat done in aluminum to bring it back down to its original lines. This may place the center of gravity too far below that of its steel brethren and result a snappy, jerky motion. So instead, you may want to place some of the added weight higher up. But again, best advice is to consult the boat’s designer.
Aluminum is not as strong as steel so some compensations must be made if using it in place of steel. Without getting too technical, with aluminum used for shell plating (e.g., 5086-H116) compared to mild steel, yield strength for aluminum as-welded is about 25% to 35% less than that of steel. In addition, it has about 75% the tensile strength at 1/3 the weight. Put another way, to get the same strength as steel in an aluminum hull, it needs to be approximately half the weight of steel.
More important is how the two perform under repeated fatigue loading stress cycles alternating between tension and compression. Tests show that for a similar number of cycles, steel stays above its yield strength threshold. But aluminum dips below it, suffering a loss so that strength is equivalent to only 75% of its yield stress. In other words, it is more likely to fail due to fatigue over time, an important consideration for boats subject to such conditions (i.e., high-speed powerboats). The point is that if you decide to adapt a steel design to aluminum, you’ll need to increase scantlings (i.e., the sizes of hull members). But by how much?
Converting from steel to aluminum is fairly straight-forward mainly because the members used are much the same in configuration and the methods of design and construction are similar. And while there are standards-making organizations (e.g., A.B.S.) with rules and formulae that can be use for determining a boat’s scantlings, a more-pragmatic approach for the less-technically oriented is to use the following rule-of-thumb. After all, we’re talking relatively small boats here, and as we’ll see, the sizes, types, and thicknesses of members readily available and suitable put some practical limits on what can be used to frame up and plate a metal boat in the first place.
Consider plating thickness. On the steel boat, this is more often based on the practical minimum necessary to ward off corrosion over time, provide decent welds, and a thickness adequate to minimize unsightly deformation. Thus 10GA (.1345″) plating is commonly specified as a minimum in small steel boats even if something thinner might suffice if strength alone were the requirement. (NOTE: Many of our steel “SHRINK-WRAP” designs can effectively use steel much less than 10GA, such as 11GA and 12GA.)
So in light of the above about the materials, and based on experience over time, aluminum members that are 30% to 50% larger than steel members will suffice for most small boats up to about 40′. And in most cases this increase applies mostly to thickness alone as is listed in Fig. 2 showing sections for a typical planing utility power vessel of chined form.
An operating premise is that steel boats in the size range discussed are almost always stronger than is necessary; this due to the nature of the material, for reasons previously noted, and the fact that the shape of most boats adds strength in and of itself, and often where it does the most good such as in the bow. Thus there is some latitude in the conversion process – we’re not talking rocket science here.
So using the example, 10GA (.1345″) bottom plating in the steel boat, and applying our rule-of-thumb, results in a nominal 3/16″ (.190″) plating thickness in aluminum, or just over 40% thicker. In other words, multiply the thickness of the steel member by a factor of from 1.3 to 1.5 to arrive at the thickness required in aluminum. (Tip: Start with 1.4 and round up or down to suit material availability or to have a boat that is lighter and a bit less strong or heavier/stronger respectively). That’s basically all there is to it.
Fig. 2
Fig. 2 – Half-sections show originally specified scantlings for a 26′ planing utility boat in steel and modified scantlings based upon the rule-of-thumb explained in the text and that might be used if the boat were built in aluminum. In the listing, a (*) for the aluminum version indicates optional material that might be substituted in place of the specified extrusion if the shape and/or size is not available or is too costly. The point is, many alternatives can be used to build an aluminum boat with largely the same results in terms of strength, durability, etc.
F.B. = Flat Bar
KEY | MEMBER | STEEL | ALUMINUM |
---|---|---|---|
A | Bottom plating | 3/16″ | 1/4″ |
B | Side plating | 10 GA. | 3/16″ |
C | Keel | 3/8″ | 1/2″ |
D | Bottom frame | 3-1/2″ x 1/4″ F.B. | 2-1/2″ x 1-1/2″ x 1/4″ Angle (*) 3-1/2″ x 3/8″ F.B. |
E | Side frame | 3″ x 3/16″ F.B. | 2-1/2″ x 1-1/2″ x 3/16″ Angle (*) 3″ x 1/4″ F.B. |
F | Side deck beam | 2-1/2″ x 3/16″ F.B. | 2″ x 1-1/2″ x 3/16″ Angle (*) 2-1/2″ x 1/4″ F.B. |
G | Bottom longitudinals | 1-1/2″ x 3/16″ F.B. | 1-1/2″ x 1-1/4″ x 3/16″ Tee (*) 1-1/2″ x 1/4″ F.B. |
H | Side longitudinals | 1-1/2″ x 1/8″ F.B. | 1-1/2″ x 1-1/4″ x 1/8″ Tee (*) 1-1/2″ x 3/16″ F.B. |
I | Sole longitudinals | 1-1/4″ x 1/8″ F.B. | 1″ x 1″ x 1/4″ Angle (*) 1-1/4″ x 1/4″ F.B. |
J | Coamings | 3″ x 1/8″ F.B. | 3″ x 3/16″ F.B. |
K | Motor girder | 10 GA. | 1/4″ min. |
L | Motorflange | 2″ x 3/16″ F.B. | 2″ x 1/4″ to 3/8″ F.B. |
M | Floors | 10 Ga. W/1-1/2″ Flange | 1/4″ with 1- 1/2″ Flange |
N | Sole beams | 2-1/2″ x 3/16″ F.B. | 2″ X 1-1/2″ x 1/4″ Angle (*) 2-1/2″ x 1/4″ F.B. |
O | Sole | 10 GA. | 3/16″ |
P | Stanchion | 1″ Pipe | 1-1/2″ Pipe |
Q | Rub rail | 1-1/2″ Sche. 40 Pipe | 1-1/2″ Sche. 80 pipe |
R | Side deck | 10 GA. | 3/16″ |
In the above and referring to Fig. 2 for a steel vessel, the internal framing shows simple members such as flat bar stiffeners, etc. These members are common in steel boats rather than using formed or extruded members such as angles, channels, tee’s, etc., for a couple of reasons. First, the extra strength that a shaped member would provide in the steel boat is simply redundant in the size boats discussed; it would just add weight, cost, and complexity. Second, shaped members add to the difficulties of inspection, maintenance, and corrosion protection in the steel boat; for example, the ability to see and coat the underside flanges is difficult, especially when such members are small.
However, in the aluminum boat in Fig. 2, shaped, formed, or extruded members are shown for many members along with options for flat bar and/or plate members for comparison purposes that might also be used as a lower-cost alternative. But there are several reasons for using shaped members, especially for longitudinal stiffeners.
First, such members are stronger. Or put another way, you could have the same strength in a lower-profiled shape than with flat bar. And the added strength in the aluminum boat is a plus. Another benefit might be more usable interior volume. And because marine aluminum requires no corrosion resistant coating and won’t rust, the shaped members don’t add to maintenance and inspection difficulties as in the steel boat.
Finally, shaped members, especially those of symmetrical section such as tee’s and channels, are easier to work. They tend not to be so floppy, and bend more uniformly than flat bar. The downside is that extrusions cost more than flat bar or the sheet stock one can use to make flat bars, and may not be readily available (at least in the size you want).
If working from stock plans for an aluminum boat, the designer probably specified certain sizes, types, and alloys of members for framing, etc. However, it’s possible that not every item will be available from your supplier or at a reasonable price. But deviations may be possible. Most designs have some latitude in alternates that can be substituted. It’s simply not practical for a designer to specify each and every option.
For example, angles can be substituted for tee’s and vice versa. Channels can be made from split square or rectangular tubing, or even split pipe if somewhat larger than the specified channel. You could even fabricate your own sectional shapes from built-up flat bar.
Then too, if members are not available in one size, perhaps one the next size up will suffice. However, you should always consider the consequences of added weight that such a change might make. Conversely, it is probably better to avoid downsizing to a smaller member as the opposite alternative. But you may compensate for using smaller members by placing them closer together, for example, in the case of longitudinal stiffeners, and/or you might space frames more closely together all in an effort to reduce the area of unsupported plating.
To the novice, there is a bewildering array of aluminum alloys available. But for the welded aluminum boat, the choices narrow down to the so-called marine alloys in the 5000 and 6000 series, the latter typically being extrusions. Yet even within these series there are still many alternatives. But the most common, readily available, and suitable for welded boat hulls include:
5052-H32
5052-H34
5083-H321
5086-H32
5086-H112
5086-H116
6061
6063
With these choices, you should be able to find everything you’ll need to build your own boat. The 5052 material is less costly than 5086, but has less tensile strength (about 20-25% less) temper for temper. However, the designer may have already taken this into consideration if 5052 is specified. Corrosion resistance for the 5000 alloys listed above is excellent in all cases.
The 6061 material has good corrosion resistance also and is commonly used for extruded shapes. The preceding is not to imply that other alloys and/or tempers within the series may not be suitable; check with your supplier for recommendations on alternatives in such cases. Many have substitution guides you can use to suit what’s stocked.
Early aluminum boats were often made with closely-spaced transverse frames with few, if any, longitudinals, a carry-over from traditional wood boatbuilding no doubt. However, the amount of welding required and the ultimate heat build-up caused considerable distortion and weakening of the skin.
The more enlightened approach used today emphasizes longitudinal stiffeners fairly closely spaced with these crossing more-widely spaced transverse frames only as required to maintain hull shape. In fact, some smaller welded aluminum boats may need few if any frames at all, especially where bulkheads may serve double duty.
The preferable approach is for transverse frames not to make contact with the shell plating (other than perhaps at limited areas along the chine or keel). In effect, such frames are “floating” within the hull, and are used to support and reduce the span of longitudinals which are the primary members stiffening the hull plating.
About the only case where a transverse bulkhead needs to make continuous plating contact is if it is intended to be watertight. Even then, such a practice tends to distort the plating and is often readily visible on the outside of the boat. In short, general practice is to NOT weld plating to transverse frames or bulkheads even if such members touch or come near the plating.
The chine is the junction between the bottom and side on a v-bottom or flat bottom boat. On high-speed planing boats, this corner should be as crisp are possible, especially in the aft half of the hull. The reason is that water should break free from the hull to reduce frictional drag at speed, and not climb up the topsides.
As shown before, Fig. 1 includes several possible chine configurations, with and without backing members as discussed previously. Backing members (such as in ‘C’ and ‘D’) help tie frame members together when setting up and help define the chine line to assure a smooth, fair curve. Otherwise, a backing member is largely optional.
If a special extrusion as discussed before is available, these are acceptable. The example in ‘E’ includes a built-in spray deflector, and can be bent along its length as required to conform to an ever-changing angle between the side and bottom that commonly occurs. Side and bottom plating fit into the slots which are then welded continuously. Whether such welding is done both sides depends on plating thickness and a builder’s desires. From an appearance standpoint, a continuous inside weld looks best.
However, such extrusions are often proprietary items or otherwise prohibitive in cost, and a problem to buy and ship in small quantities. Completing the ends of such extrusions where they join to transom and stem areas is also not always easy for the builder making a single boat.
An alternative that provides much the same effect is the tee-bar in ‘C’; this is easy to bend and is usually readily available. However, if the protruding flange is too pronounced, there may be a tendency to hang up on rocks in certain boats such as whitewater boats, or snag debris and catch pilings in other types of boats depending on their use.
A lower cost alternative is a simple round bar in ‘D’; this adds abrasion protection to an often vulnerable corner. But if too large a diameter, won’t provide the crisp edge needed for higher-speed planing boats (you could add a flat bar deflector edge-wise against the bar slightly above the corner that might help, however). Otherwise, round bar bends around frames easily and gives a well-defined boundary to work to when fitting side and bottom plates.
A simple corner joint with side and bottom butting together as in ‘A’ is technically feasible, but is more difficult to fit and make fair. A temporary chine backing member may help in this regard. If the plating is thin, say 1/8″ or less, take care when welding to prevent blow-thru, and use equipment suitable to the task.
A modification with integral spray deflector/lift strake that’s ideal for high-speed work is shown by ‘B’. In this case the bottom is fitted first and cut with care along the chine line (a temporary backing member may aid in fitting). Then topsides are installed, letting the edge overhang the junction a distance as required to form the spray deflector flat. While a good design, this configuration also takes care to assure fair lines.
As mentioned, on the modern aluminum hull, most plating is reinforced by longitudinals. Fig. 3 shows several member configurations that can be used. While a good set of plans will specify what to use for these members, this does not necessarily rule out another alternative if what is specified is not available.
Fig. 3
The cheapest and most easily obtained is the simple flat bar (‘A’). These are available in many sizes, often in the form of extrusions with radiused edges that facilitate welding, or you can cut your own from plate. Thicknesses of 1/4″ or more tend to bend more readily without distortion, or you can cut to curvature from plate. For strength comparable to other shapes, such as tee’s, flat bar needs to be wider and thus tends to encroach more upon the hull interior.
Other stiffeners are often extruded shapes that can get costly and may not be as readily available in the sizes needed. Angles as in ‘B’ are usually easy to get and have good strength to weight, but the asymmetrical shape may make bending in two planes difficult. Tee’s (‘C’) present a symmetrical shape that forms more easily.
Inverted channels (‘D’) are also an effective stiffener, but rectangular tubes (‘F’), and “I’s” (‘E’) are largely overkill since that portion of the member against the hull adds weight with little or no gain in strength, but at a higher cost. In other words, don’t use unless nothing better is available.
On the other hand, the special hull stiffening channel configuration sometimes available as in ‘G’ makes an effective stiffener. A less effective member strength-wise is the split pipe or tube as in ‘H’ which is sometimes also stocked as a ready-made stiffener.
When installing longitudinals, bending can present problems depending on curvature and member type. One approach some builders take to reduce bending effort is to gore members along their flanges as in Fig. 4 below. This idea is sound, but the execution takes care to assure fair curves. Good practice also calls for radiusing the corners at the gores slightly to minimize hard spots against the plating. Avoid over-welding, and completely around the ends of each cut.
Fig. 4
For powerboat transoms – especially those using outboards or I/O’s that transfer thrust to the transom – bottom plating should extend past the transom plating by at least twice the plating thickness (see Fig. 5B below). This allows a strong fillet weld on both sides of the junction (the inside weld can be intermittent). A simple corner junction here as in Fig. 5A below is harder to fit and the corner weld ultimately weaker.
Fig. 5
In fact, some builders extend the bottom plating considerably past the transom on faster planing hulls to form integral non-adjustable trim tabs. These can later be bent down slightly if required for best performance and then bracketed to the transom once an optimum position has been found.
Transom thickness technically need be no more than that of the side or bottom plating. But in the case of outboards or I/O’s, plating should be a minimum of 1/4″. Additional thickness may be required – at least in the area of the cut-out – either through the use of doublers or thick inserts.
A thicker insert is preferable at a cutout to avoid the need to seal joints between doublers by welding. Where thin plating meets thicker plating, bevel the thicker edge at a slope equal to at least three times the thickness of the thinner plate (see Fig. 6.). The insert should have rounded corners rather than being a hard square or rectangular shape.
Fig. 6
There is an on-going debate as to whether welded aluminum boats should be made as light as possible via light plating and framing (but with more of it), or with heavier plating using minimal but also somewhat huskier framing members. To put this issue in perspective, we’ll assume strength is sufficient in both cases in order to examine the merits otherwise.
A boat built with light plating and framing is lighter in weight for more-economical operation, has a higher speed for a given power, is more-easily trailered, has greater payload, and because it has less material, will cost less.
Advocates of heavier plating and framing counter that thicker plating is stiffer which better resists flexing, twist, and fatigue, won’t dent as easily, and will deter longer any effects of corrosion. They also claim that lighter scantlings take more time and labor to build (more members to cut, fit, and weld), and that any increase in weight and/or cost is offset (at least to some extent) by a reduction in framing. Then too, they claim thicker plating is less prone to distortion by welding heat and it’s easier to make stronger joints since it’s more likely that both sides of joints can be welded without problems or defects. In addition, thicker members are often easier to handle and work since they resist distortion and are not so “floppy”.
Who’s right? As a designer I feel there’s validity in both camps, but with some qualifiers. First, there is a natural tendency among builders in any material to over-build and second-guess the designer, even when a boat uses the heavier plating approach initially. The typical idea is that if so much is good, then a little more must be better. The result is that such boats weigh more than the designer predicted. And who gets the blame when the boat doesn’t perform up to predictions? You guessed it – NOT the builder.
Consider. A seemingly innocent plating increase of 1/16″ for a boat originally specified for 1/8″ (.125″) sheet results in a 50% increase in plating weight. Or for the boat specified with 3/16″, another 1/16″ (to 1/4″ total) adds 1/3 more plating weight (perhaps 400 lbs. or so for a boat in the 25′ range). Conversely making frames from 1/4″ material versus 3/16″ won’t add but a few pounds, and could also make construction easier.
In other words, I’d favor the latter change but might question a plating increase. Much depends on the boat and its expected service. For pleasure boats, I tend to favor lighter scantlings, but for more rigorous duty, heavier construction may be justified. However, rather than simply increase plating thickness, you might get similar results by adding a few more internal stiffening members instead.
An appealing possibility on metal boats is tanks integral with the hull, which is acceptable for diesel fuel but not gasoline. Because the hull shell plating provides one or more of the tank sides, and internal tank members can double as hull stiffening members, such tanks can save material and add capacity without taking up more room. However, I favor separate tanks for boats less than about 40′ for the following reasons.
First, tanks might be of such a size or located in such a position that welding tight seams all around the perimeter is difficult if not impractical. Second, because full welds are required, there is a greater chance of heat buildup and ultimate hull plating distortion. Finally, special consideration must be given at the intersections of tank ends, hull stiffening members, and internal tank baffles when required. Attempting to fit and weld tank ends tightly around stiffeners that pass through the tank is tedious if not impossible. Instead, hull stiffeners should stop at tank ends, with similar members cut and fitted inside, or with internal baffles installed in line with such stiffeners as substitutes and to maintain continuity.
Conversely separate tanks built outside the hull are physically easier to manipulate during assembly and welding, easier to test and assure integrity, easier to repair or replace, and not as likely to suffer damage in a collision. Aluminum tank thickness is sometimes shown as a function of tank capacity such as the following:
To 50 Gals: .090″
50 to 80 Gals: .100″
80 to 150 Gals: .125″
However, for practical purposes, most tanks should be at least .125″ thick, and for larger tanks, 3/16″ material may be justified from a strength standpoint and because it’s easier to weld both sides of joints. Thicker tanks also require less stiffening, and since plating material is usually suitable, no special thinner stock need be ordered as might be implied from the above list.
Water and waste holding tanks should be coated on the inside to prevent corrosion from impurities and the effects of aluminum hydroxide precipitation that can turn water “milky”. Also provide striker plates or doublers on the bottom under sounding tubes (if being used) to prevent damage to the inside of the tank. All tank tops should be canted, sloped, or cambered so condensation or moisture will drain off the tops. Tanks can be made out of the same material used for the hull plating (5052, 5086, etc.).
Special computer-aided design programs coupled with numerically-controlled cutting equipment have made it possible to literally pre-cut all the components of a metal boat to precise size and shape in kit form ready for final welding assembly. However, for successful results, a skilled boat designer familiar with the material and fabrication techniques, along with the ability to operate the software to within exacting tolerances is a prerequisite.
Otherwise, as they say, a miss can be as good as a mile. If one major component is not spot-on, you could waste a lot of costly metal quickly and perhaps assemble a boat that could be so inaccurate as to suffer severely performance-wise. But done right, the system has inherent appeal since such boats should be easier and faster to assemble.
Is this technology suitable for the do-it-yourselfer building just one boat? It depends. The ability to provide such a technologically-advanced product does not come cheap. The design process usually requires an entirely different building and assembly system than would be the case for a “one-off” which may use simple, traditional framing, is more-costly, and often takes more time than traditional design methods even though a computer is used and necessary.
For the production builder, the higher design and development costs will be amortized over a great number of boats. And the labor savings would no doubt make up the investment manifold over time.
But it’s not as straight-forward for the average do-it-yourselfer looking for a stock plan or kit. First, usually such designs are proprietary; that is, the rights are owned by a boatbuilding firm who commissioned the project and is unlikely to have any interest in sharing their design or making it available as a “stock design” to anyone else. Second, facilities for pre-cutting metal boats are currently far and few between, and not all have equal capabilities and expertise when it comes to boats. Third, if a do-it-yourselfer is not near such a facility (assuming a design is available), shipping costs can be prohibitive on just a single unit. Finally, although there are some designs available (often because a builder gives up his design rights for one reason or another), design choices are minimal.
A design where you build from scratch and cut out your own parts may take somewhat longer to build, but will be the low-cost alternative. Also, pre-cut kits typically allow little, if any, leeway to make changes – something that’s easy to do when building from scratch. And there are countless stock plans to choose from, many at a low cost.