Thunderbolt by Bob Atwater, Seneca, South Carolina
16 November 2010 Update (Cont'd)
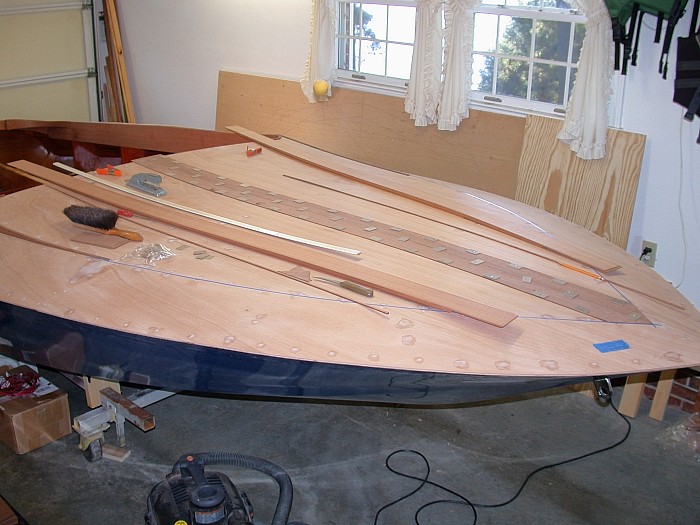
This begins the planking. I cut the planks (3.25 " wide
by 3/16") on my 14 " band saw using a super sharp
½" resaw blade and a homemade jig. Actually, I
wore out two blades sawing some 400 feet or more of planks.
The darker planks are sepele (dark mahogany type wood) and
the lighter planks are Honduras mahogany.
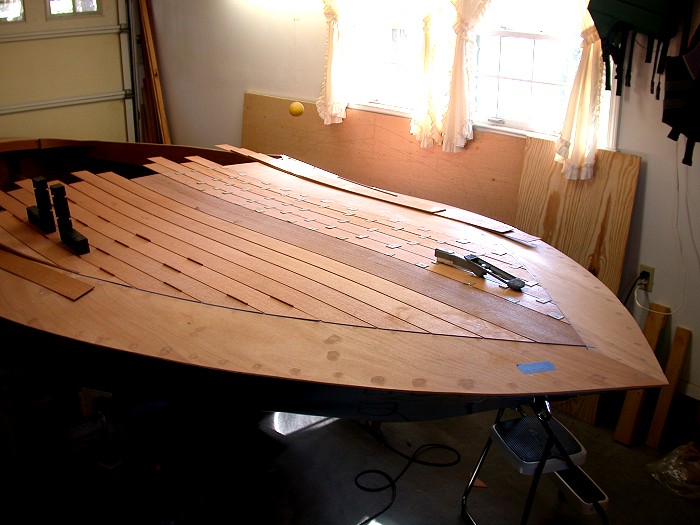
The planks are bookmarked from the center out. After gluing
the two center planks on the plywood deck with epoxy I worked
with four planks at a time moving out to the side. The
spacing between planks is about 3/16".
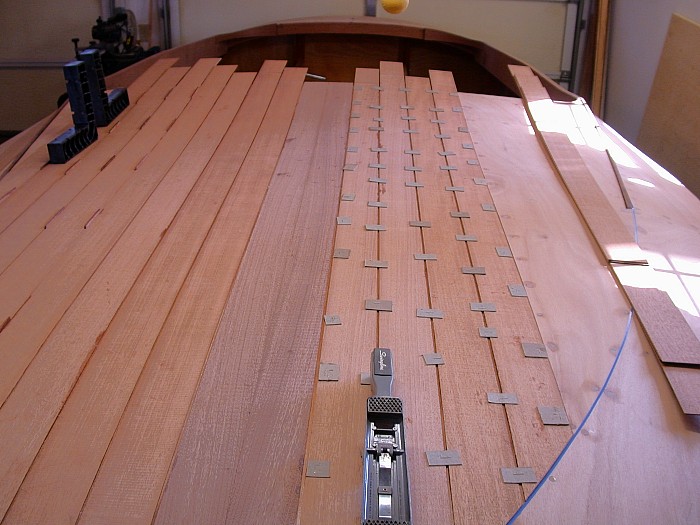
After some experimenting, I ended up using a standard
Swingline paper stapler driving staples through small squares
of cardboard to hold the planks in place while the epoxy
cured. While the stapler worked on the Okume plywood, it
would not work on fir or birch plywood (surface too hard?).
After removing the staples I put a drop of water on each
small hole created by the staples. Once sanded, the holes
were no longer visible.
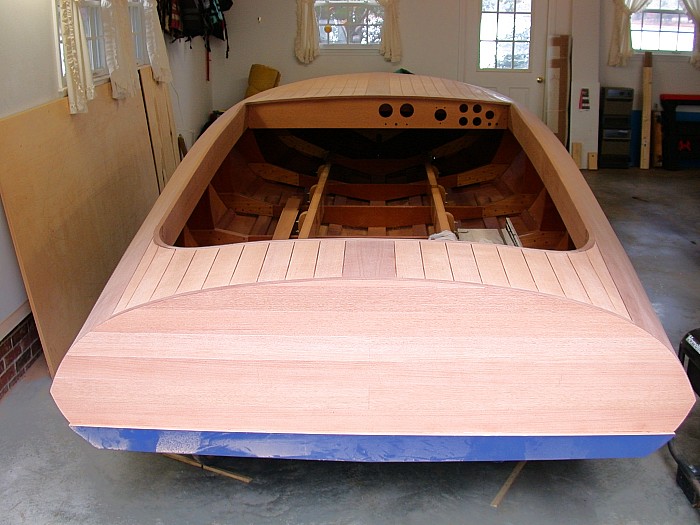
The transom was planked without spacing. Sepele was used for
the coaming. The corners connecting the coaming with the rear
deck facing board were made by laminating six thin pieces of
sepele around a 12 inch radius.
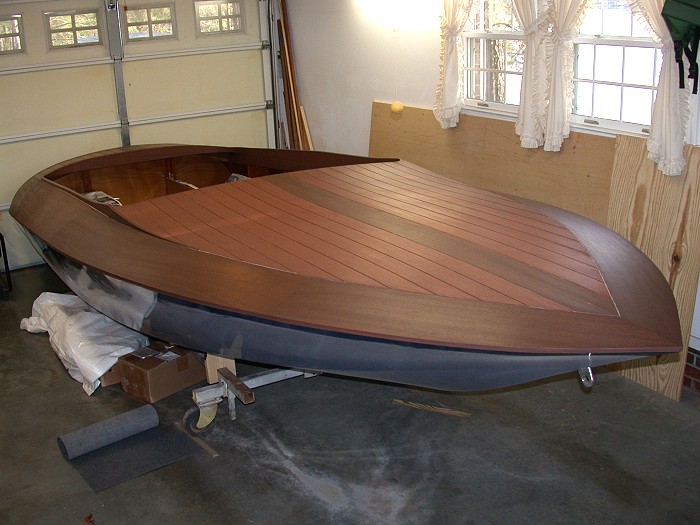
I used Sandusky Chris Craft filler stains. The Sepele planks
were stained with a mixture of two parts walnut and one park
mahogany stains. The Honduras mahogany planks were stained
with two parts mahogany and one part walnut.
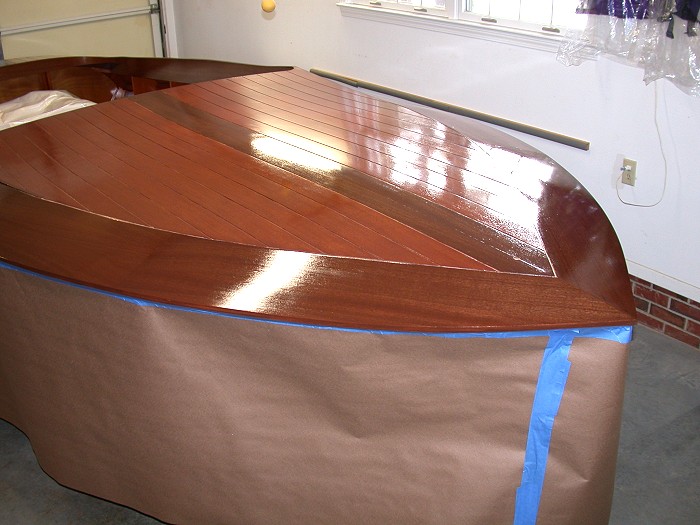
First coat of Petit Old Salem clear sealer.
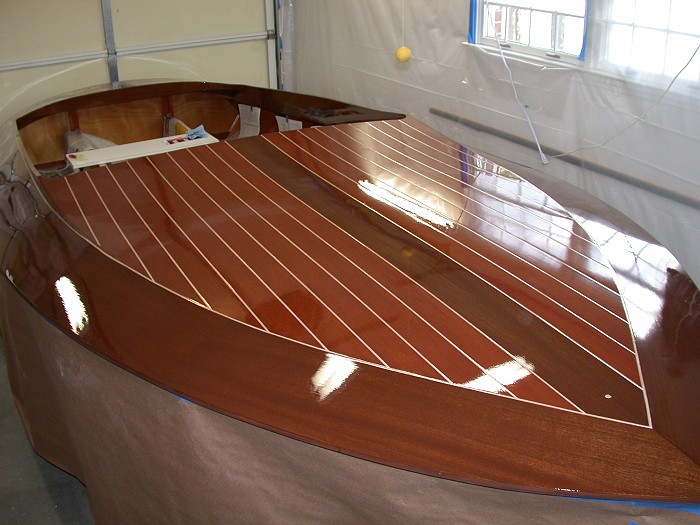
After 6 thin coats of Interlux varnish, the seams were filled
with tan 3M 5200 adhesive/sealant. Other sealers were easier
to work with. However, I could not find a light tan color
only white which was too much of a contrast. Each seam was
masked off. After filling carefully to minimize air bubbles,
a 5/8-inch dowel was drug down the seam to provide a slight
concave surface in the sealant. The masking tape was then
removed and a soft plastic scraper was used to remove any
excess 5200 materials on the planks. Occasionally, follow-up
with a soft cloth and solvent was necessary. I practiced on a
mockup for quite awhile before going for real on the hull.
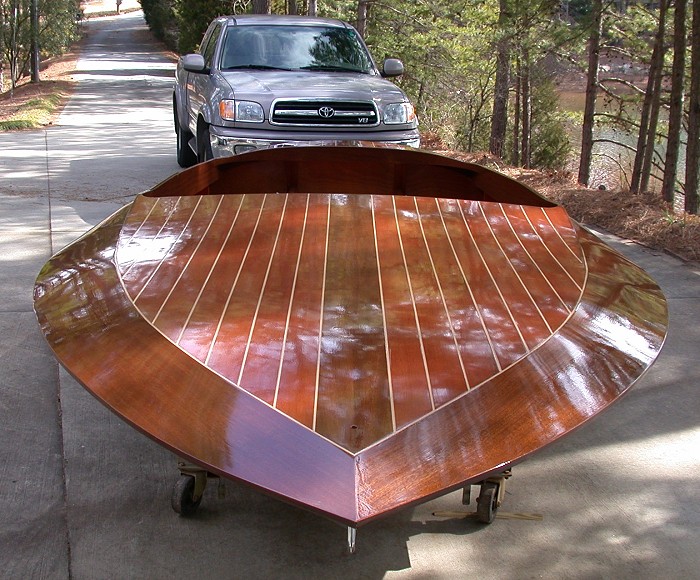
There are six more coats of Interlux varnish over the decks
and the 5200 in the seams. I sanded lightly between each coat
of varnish. After every three coats, the sanding was fairly
aggressive trying to obtain a smooth true surface. Following
the 12th coat of varnish, I finished sanding with 2000 grit
followed by buffing with 3M Finesse II and a power buffer
with a 8 ½ inch foam bonnet at slow speed (less than
1700 rpm).
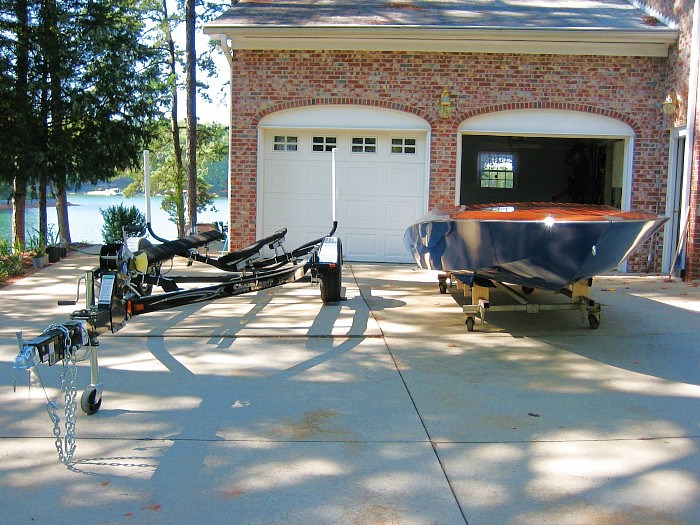
Time to move the hull to a new Shorelander trailer.
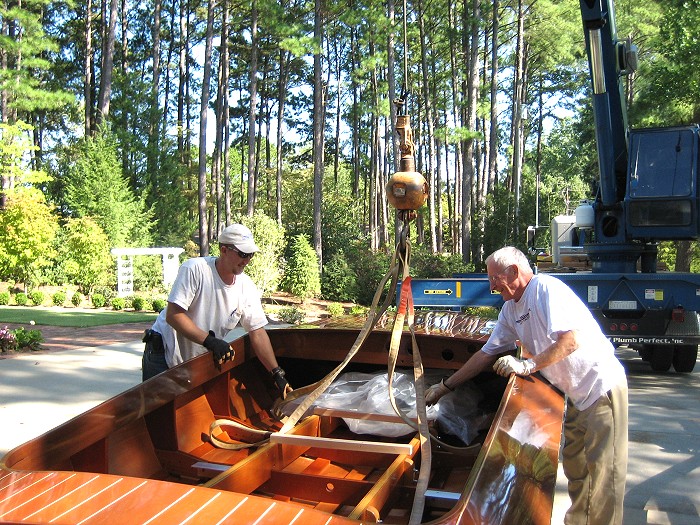
A 34-ton truck crane is a little overkill, but it sure beats
a half dozen guys drinking beer.
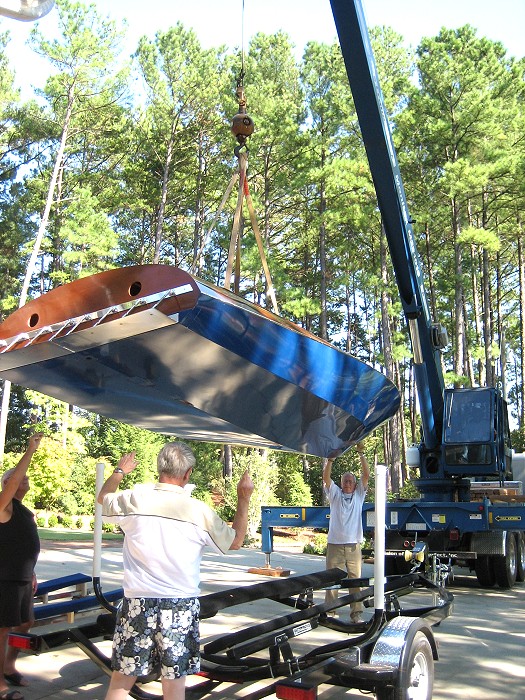
I am the old guy at the front that will not let go of the
boat.
Continue
|