10-28-03
Barry, some significant progress on the Sissy-Do has been made!
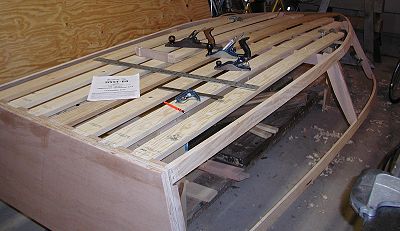
Picture 7 (Fairing Tools) October 11, 2003
The bottom edge of the chines must be level with the bottom surface of the battens and keel. The tool of choice is a wood plane, either a block plane or a longer jack plane. Occasionally a shorter hand plane will work, also. A good straightedge is also required to be able to compare the chine surface to the keel and batten surfaces. Fairing requires a lot of checking the fair and a little planing of the chine to make it fair. When I find that I have planed a section of the chine to a state of fair, I mark it off with a pencil so that I do not accidently go over that area again with the plane and ruin its degree of being fair. Incidently, never set a plane down on a hard surface with the plane resting on the edge of the blade, it can nick or dull the edge.
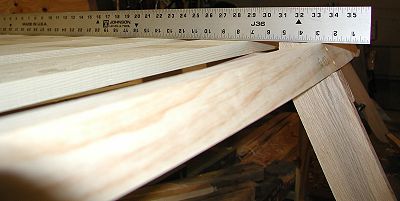
Picture 8 (Fairing The Chine): A check with the straight edge shows that this area of the chine is fair with the keel and battens, good progress. I mark this area with a pencil so I don't go over it again and perhaps ruin the degree of being fair.
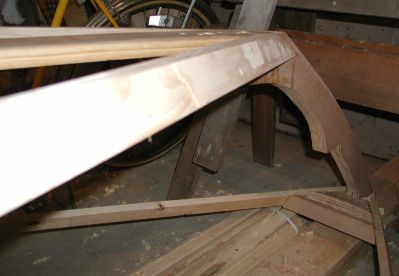
Picture 9 (Chine Is Faired): All of the chine, from stern to bow, must be fair with the keel and battens in order to get a good joint between the bottom planking and the chine. The chine acts as a joint to fasten the bottom to the side and as a seal to keep the water out of the boat.
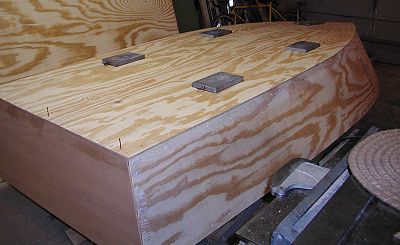
Picture 10 (Bottom Is Fitted) October 18, 2003:
The bottom has been fitted to the boat framing. I layed the main sheet of plywood on the boat frame and traced around the frame with a pencil. Then placed the bottom sheet on a couple of sawhorses and cut along the tracing with my sabre saw. After I cut out the bottom to the needed shape, I placed it back on the boat frame, aligned it correctly with the frame and weighted it down with some lead weights I had (full gallon cans of paint would have made good weights also). Then I located all of the screw hole locations into the transom and chines to fasten the bottom planking. Countersunk screw holes were then drilled three inches apart for all of the screws
except on the keel and battens where the screws were to be twelve inches apart. I inserted eight perry nails into the holes in the transom and stem to keep the bottom planking from shifting around as I worked.
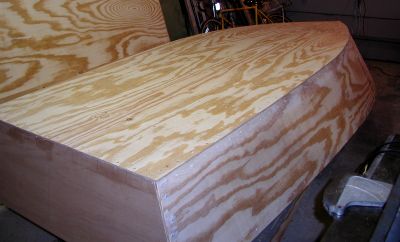
Picture 11 (Bottom Is Done) October 26, 2003:
This photo show the bottom after is has been fastened down with marine epoxy and wood screws, the screws being brass no. 8 x 1" long. The epoxy had a working time of roughly fifteen minutes, which prevented any picture taking while that work was going on. My wife helped by mixing and applying the epoxy while I spread it along the boat member surfaces with a serrated edge spreader. Then, together we lifted the main bottom piece over the frame and set it down. Quickly, I adjusted its position and inserted locating pins (eight penny nails) into strategic holes in the transom and stem to keep the bottom from sliding around. The lead weights were placed back on the plywood to help hold it down. My wife, Kathy, inserted the screws in the holes as I screwed them home with a screwdriver bit in my variable speed drill. This went quickly and we finished before the epoxy had even started to get stiff. Afterwards, I checked all of the screws for being tight with a hand screwdriver.
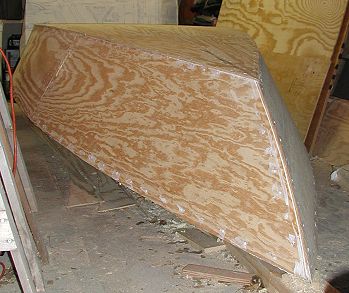
Picture 12 (Bottom Done Bow2) October 26, 2003:
The bottom is installed! Now I have to wait for the epoxy to set up and cure, some breathing time. I have used the hand plane to trim up the leading edge of the bow. That work turned out very nice. I will use the hand plane to trim the edges of the bottom sheet to the sides, and round the edges slightly. Then, I will apply epoxy to all of the slightly countertsunk screwheads and sand that down, followed by a coat or two of sanding sealer and then final sanding of the hull exterior. I will fiberglass tape all of the seams and perhaps the entire hull exterior, before turning the boat right side up to finish the interior.
George Maher, Fargo, North Dakota
Continue |