Boatbuilding with Plywood
Chapter 6 - Fastenings
Continued
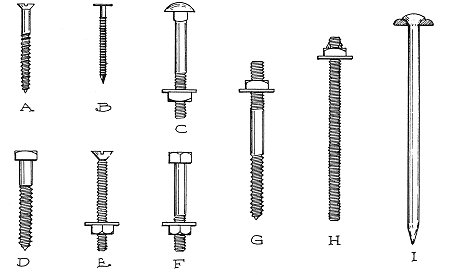
Plate 6A - Fasteners commonly used in plywood
boatbuilding include: (A) Flat head wood screw, (B) Ring shank boat nail, and
(C) Carriage bolt. Other incidental fastenings may include: (D) Lag bolt, (E)
Flat head machine screw, (F) Machine bolt, (G) Hanger bolt, (H) Threaded rod
with nut jammed on to form a through-bolt, and (I) Drift with clenched head and
ring or washer.
FASTENING MATERIALS
Basically, metal fastenings can be broken down into
ferrous (containing iron) and non-ferrous types, which do not contain iron. As
most people realize, ferrous metals such as iron and steel will rust when
exposed to the elements, and especially so in a salt water environment.
Consequently, ordinary steel fastenings have no place in boatbuilding. However,
a certain amount of rust and corrosion protection can be given to ordinary
steel fastenings by various plating techniques.
One plating technique consists of an electroplating
method, which deposits a thin layer of cadmium or zinc onto the metal's
surface, and this tends to inhibit the formation of rust to some extent.
However, driving such a fastening almost immediately destroys the very thin
layer and rust occurs almost as quickly as if the coating didn't exist.
These electroplated type screws therefore offer poor rust resistance under salt
water or even exposed conditions. Their main advantage is that they won't
rust on the hardware dealer's shelf.
A better coating process for steel fastenings is a
hot dipped galvanized coating of zinc where the fastenings are immersed in
molten zinc thereby depositing a heavy zinc-rich coating onto the fastening.
Hot dipped galvanized fastenings do not rust when exposed to the weather,
however, they may be subject to galvanic corrosion below the water line in salt
water conditions when located adjacent to dissimilar metals.
For a boat that will remain for long periods in
salt or brackish waters then, hot dipped galvanized fastenings should not be
located side by side with bronze or non-ferrous fastenings or fittings since
the less noble metal (in this case, the steel fastenings), will begin to
deteriorate. It is possible, however, to use the bronze fastening below the
water and the hot dipped galvanized fastening above the waterline. For a
trailerable boat or for one that will not remain in salt or brackish waters for
long periods, the hot dipped galvanized fastening is entirely suitable,
especially for boats covered with fiberglass.
Non-ferrous fastenings for boats usually include
brass, bronze, and Monel metals, all of which are copper-based. The brass
fastening is often considered corrosion resistant, however, this is not
actually the case in a marine salt-water environment. Such a fastening will
dezincify, which means that the zinc content will leech out of the fastening
causing it to rapidly disintegrate. Besides this, brass fastenings are
inherently weak, with the heads of fastenings being easily wrenched off when
driven hard or otherwise popping off under stress. Because of these problems,
brass fastenings are not recommended, with the possible exception of
non-structural joinerywork where strength or corrosion resistance is not
important.
Bronze and Monel fastenings are superior
fastenings, especially for use below the waterline in boats that will remain in
salt or brackish waters. There are many different grades of bronze, however the
silicon-type is probably best suited for fastenings. Of course, bronze and
Monel fastenings are expensive, but as a total percentage of the cost of the
boat, the price is only a small fraction. One must consider also that the extra
cost of bronze fastenings will probably be more than repaid by the higher
resale value of a bronze fastened boat when it is sold.
Aluminum fastenings are also considered as
non-ferrous fastenings, however, since they are weak and not corrosion
resistant, they also have no place in plywood boatbuilding for structural
use.
Many people are under the impression that stainless
steel is an ideal fastening material. While it is true that stainless steel is
ordinarily highly rust resistant, it is not totally free from corrosion. When
stainless steel is placed under poorly aerated water conditions or otherwise
shielded from air, even by having just a thin oil coating, galvanic action can
occur, especially when adjacent to dissimilar metals in salt water. This
corrosion usually begins as a very small surface pit trapping salt water, which
gradually corrodes away to the inner portions of the fastening. Such corrosion
is called crevice corrosion and can dissipate a fastening or fitting in the
most devious way; from the inside out where it may not be detected until it is
too late. The tendency for crevice corrosion to occur will vary depending on
the grade of stainless steel. Some grades are more susceptible than others.
However, because of the wide array of stainless steel types, and the fact that
it is often difficult for the novice to know which type he may be getting, it
is usually prudent to avoid stainless steel fastenings for the most part. They
are expensive as well.
Continue
|